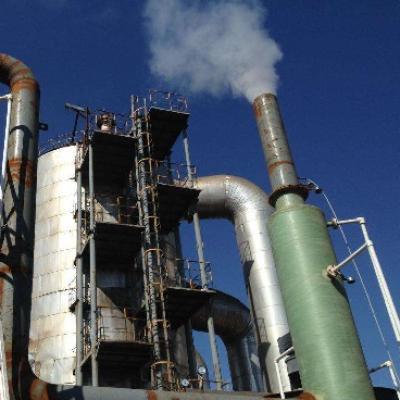
Desulfurization and dust removal solutions
Date:2023-01-06 10:59:57 Hits:1080 Belong to:Industrial production
At present, countries all over the world attach great importance to flue gas desulfurization and have developed dozens of effective desulfurization technologies, among which the widely used flue gas desulfurization technologies are: (1) lime/limestone - wet method. (2) Rotary spray semi-dry method (LSD). (3) Calcium-in-furnace spraying and humidification activation method (LIFAC). (4) Seawater flue gas desulfurization method. (5) Ammonia flue gas desulfurization method. (6) Simple integrated wet FGD technology.
Lime / limestone - gypsum wet method, with a wide range of applicable coal, cheap and easy to obtain raw materials, high desulfurization rate (up to 90% or more) and many other advantages, occupy the largest market share, but the investment and operating costs are large, and the amount of operation and maintenance. The rotary spray method has a lower desulfurization rate (up to 80%-85%) than the wet method, and the investment and operation costs are slightly lower than those of the wet method. The product is calcium sulfite (CaSO3). Calcium spraying tail humidification method in the furnace, the desulfurization rate can reach 70%-80%, and the engineering cost is lower. The product is calcium sulfite (CaSO3), which is easy to cause slagging in the furnace. Seawater flue gas desulfurization technology, simple process, reliable system operation, high desulfurization rate (up to 90% or more) low operating costs. However, the desulfurization system needs to be set up at the seaside and the seawater temperature is low and the dissolved oxygen (OC) is high. Ammonia desulfurization is usually based on ammonia as raw material, and the product is sulfur ammonia, etc. Need to be adjacent to ammonia plant and fertilizer plant. Simple wet desulfurization and dust removal integrated technology, low desulfurization rate (about 60%), lower cost raw materials for industrial waste alkali and caustic soda, need to be adjacent to a plant with waste alkali discharge, after neutralization, wastewater needs to be discharged into the sewage plant for treatment. Although the technology and device of flue gas desulfurization is improving, but in most countries, especially in the energy structure of coal accounted for a large proportion of the countries, its promotion and popularization is difficult, take our country, nearly 20 years to spend a huge amount of money to introduce technology and devices difficult to promote, huge investment and high operating costs so that enterprises carry a heavy burden, can not afford. Therefore, it is said that the technology and devices with real popularization significance still need to continue research and development.
In the current international and domestic market competition is extremely fierce conditions, to research and development of a new technology and equipment devices, so that it can be popularized on a large scale, should have the following characteristics: (1) raw materials (neutralizer) cheap and easy to obtain, high desulfurization rate. (2) engineering investment and operating costs should be low enough to apply the enterprise can afford. (3) simple process, reliable operation, easy to regulate and no adverse effects on the normal operation of the boiler. (4) to a variety of sulfur coal (oil) has a good adaptability. (5) does not cause secondary pollution, such as water pollution, dust, noise, etc.
Second, the reasoning analysis (1) raw materials (neutralizer) with the development of the market economy and social progress, the original meaning of the century-old stores are fewer and fewer, every year there are a large number of new industries rise, every year there are a large number of old industries out of the market. Flue gas desulfurization projects generally need to invest a lot of money, if the raw materials and processes depend on the adjacent factories (such as ammonia, fertilizer, waste alkali emissions, etc.), then the project is likely to stop midway due to the closure and transfer of these plants, so that the investment in the project does not get the due economic and social benefits. Therefore, limestone and lime as the neutralizing agent of flue gas desulfurization technology is recognized by most industry experts. The cost of lime as neutralizer is higher than that of limestone, and more equipment, structures and monitoring equipment are needed; the use of limestone is the most practical neutralizer because of its low cost and easy control of the reaction. The traditional "limestone - gypsum method of flue gas desulfurization" requires the grinding of limestone to 200-300 mesh, which requires the construction of a grinding station, which not only increases the investment, but also causes a certain degree of "noise" and "dust". "and dust" pollution, and its products mixed with the reactants, resulting in an increase in the calcium-sulfur ratio, increasing operating costs. If the integrated technology of desulfurization, denitrification and dust removal is adopted, desulfurization, denitrification and dust removal can be realized simultaneously in one device, which has simple equipment, small investment, low operating cost and greatly improves economic efficiency. (2) product wet desulfurization, the highest desulfurization rate (up to 90% or more), there are two kinds of neutralization products, calcium sulfate CaSO4 and calcium sulfite CaSO3, usually a mixture of two substances, neutralization products are not likely to be completely reused, if the calcium sulfite (CaSO3) once into the water, because it has a strong reducibility, will quickly deplete the dissolved oxygen in the water, so that the water fish Because it dissolves very slowly, its pollutants will exist for a long time, seriously damaging the ecological environment of the water body, so the neutralization product does not contain calcium sulfite (CaSO3) is the safest, can be reused to create value and can also be safely discharged. (3) calcium-sulfur ratio calcium-sulfur ratio (Ca/S) is an important factor in determining the operating costs, Ca/S = 1 is the limit state of economic operation, that is to say, which desulfurization process Ca/S achieve or close to 1, then it may achieve the true meaning of economic operation. In the current wet desulfurization process, the remaining reactants and desulfurization products are mixed together and excluded from separation, so it is difficult to achieve the ideal Ca/S. If the reactants exist in the state of particles, it is easier to achieve the ideal Ca/S by solving this problem, and the equipment and capital investment are also reduced, which is conducive to achieving the true meaning of economic operation.
Third, the ideal model in summary, the most ideal flue gas desulfurization process should be: (1) wet desulfurization (desulfurization rate of up to 90% or more). (2) Neutralizer is limestone. (3) Calcium to sulfur ratio (Ca/S) is 1. (4) The product is calcium sulfate and does not contain calcium sulfite impurities. (5) Low investment, simple process, low operating cost, no secondary pollution. (6) Few control parameters, mature measurement and control equipment, can realize the whole line automatic control. (7) The intermediate circulating material in operation is supplemented by boiler and power plant waste liquid, no dependence on surrounding enterprises. (8) Full absorption and utilization of flue gas waste heat.
This ideal model, if realized, is likely to become the most ideal operating mode in flue gas desulfurization technology, and its promotion and application can create huge market opportunities and social value, but it is difficult to truly realize this ideal model, mainly because: (1) limestone particles to dissolve quickly, the PH value must be less than 4, but the PH value is less than 4 when the dissolved CaCO3 on SO2 is almost not absorption. (2) SO2 dissolved in water generated H2SO3 and H2SO4 generated by oxidation, and the reaction with limestone particles generated CaSO3 and CaSO4 will adhere to the surface of limestone particles, and the more reaction pile up, making it difficult to continue the reaction. (3) CaSO4 and CaSO3 are the same absorption products, so it is difficult to make CaSO4 precipitate and not produce CaSO3. It can be said that these three problems are the real difficulties of the "limestone method" of desulfurization, and whether these three problems can be solved is the key to whether the process can achieve its intended goal and whether the device can operate stably.
Fourth, the cycle of bridge theory since it is a natural danger should build a bridge to get over it, after research found that the integration of desulfurization denitrification and dust removal technology has a bridge role. The integration technology of desulfurization, denitrification and dust removal, the environmental protection technology field of flue gas purification technology. It is through the smoke and water mixer using the principle of secondary injection of smoke into the water, the flue gas and water in the uniform dissolver will be fully and uniformly mixed and dissolved, so that the fly ash and particles in the flue gas by water moisture and precipitation, harmful gases dissolved in water, the use of chemical methods to remove SO2, NOX and dust in the flue gas. This method is achieved by the working principle diagram shown in the attached figure. It has 100% dust removal efficiency; >98% desulfurization efficiency; >90% de-selling efficiency. It has a flue gas mixer that is also an induced draft fan. It is suitable for the flue gas purification technology project of coal-fired (steam and oil) boilers and various industrial kilns, etc. The system has simple structure, low cost, high performance to price ratio, energy saving, high temperature resistance and long life.
In the current conditions of the international and domestic market competition is extremely fierce, to research and develop a new technology and equipment devices, so that they can be used on a large scale, should have the following characteristics: (1) raw materials (neutralizer) cheap and easy to obtain, high desulfurization rate. (2) Engineering investment and operating costs should be low enough to apply the enterprise can afford. (3) simple process, reliable operation, easy to regulate and no adverse effects on the normal operation of the boiler. (4) to a variety of sulfur coal (oil) has a good adaptability. (5) does not cause secondary pollution, such as water pollution, dust, noise, etc.
Second, the reasoning analysis (1) raw materials (neutralizer) with the development of the market economy and social progress, the original meaning of the century-old stores are fewer and fewer, every year there are a large number of new industries rise, every year there are a large number of old industries out of the market. Flue gas desulfurization projects generally need to invest a lot of money, if the raw materials and processes depend on the adjacent factories (such as ammonia, fertilizer, waste alkali emissions, etc.), then the project is likely to stop midway due to the closure and transfer of these plants, so that the investment in the project does not get the due economic and social benefits. Therefore, limestone and lime as the neutralizing agent of flue gas desulfurization technology is recognized by most industry experts. The cost of lime as neutralizer is higher than that of limestone, and more equipment, structures and monitoring equipment are needed; the use of limestone is the most practical neutralizer because of its low cost and easy control of the reaction. The traditional "limestone - gypsum method of flue gas desulfurization" requires the grinding of limestone to 200-300 mesh, which requires the construction of a grinding station, which not only increases the investment, but also causes a certain degree of "noise" and "dust". "and dust" pollution, and its products mixed with the reactants, resulting in an increase in the calcium-sulfur ratio, increasing operating costs. If the integrated technology of desulfurization, denitrification and dust removal is adopted, desulfurization, denitrification and dust removal can be realized simultaneously in one device, which has simple equipment, small investment, low operating cost and greatly improves economic efficiency. (2) product wet desulfurization, the highest desulfurization rate (up to 90% or more), there are two kinds of neutralization products, calcium sulfate CaSO4 and calcium sulfite CaSO3, usually a mixture of two substances, neutralization products are not likely to be completely reused, if the calcium sulfite (CaSO3) once into the water, because it has a strong reducibility, will quickly deplete the dissolved oxygen in the water, so that the water fish Because it dissolves very slowly, its pollutants will exist for a long time, seriously damaging the ecological environment of the water body, so the neutralization product does not contain calcium sulfite (CaSO3) is the safest, can be reused to create value and can also be safely discharged. (3) calcium-sulfur ratio calcium-sulfur ratio (Ca/S) is an important factor in determining the operating costs, Ca/S = 1 is the limit state of economic operation, that is to say, which desulfurization process Ca/S achieve or close to 1, then it may achieve the true meaning of economic operation. In the current wet desulfurization process, the remaining reactants and desulfurization products are mixed together and excluded from separation, so it is difficult to achieve the ideal Ca/S. If the reactants exist in the state of particles, it is easier to achieve the ideal Ca/S by solving this problem, and the equipment and capital investment are also reduced, which is conducive to achieving the true meaning of economic operation.
Third, the ideal model in summary, the most ideal flue gas desulfurization process should be: (1) wet desulfurization (desulfurization rate of up to 90% or more). (2) Neutralizer is limestone. (3) Calcium to sulfur ratio (Ca/S) is 1. (4) The product is calcium sulfate and does not contain calcium sulfite impurities. (5) Low investment, simple process, low operating cost, no secondary pollution. (6) Few control parameters, mature measurement and control equipment, can realize the whole line automatic control. (7) The intermediate circulating material in operation is supplemented by boiler and power plant waste liquid, no dependence on surrounding enterprises. (8) Full absorption and utilization of flue gas waste heat.
This ideal model, if realized, is likely to become the most ideal operating mode in flue gas desulfurization technology, and its promotion and application can create huge market opportunities and social value, but it is difficult to truly realize this ideal model, mainly because: (1) limestone particles to dissolve quickly, the PH value must be less than 4, but the PH value is less than 4 when the dissolved CaCO3 on SO2 is almost not absorption. (2) SO2 dissolved in water generated H2SO3 and H2SO4 generated by oxidation, and the reaction with limestone particles generated CaSO3 and CaSO4 will adhere to the surface of limestone particles, and the more reaction pile up, making it difficult to continue the reaction. (3) CaSO4 and CaSO3 are the same absorption products, so it is difficult to make CaSO4 precipitate and not produce CaSO3. It can be said that these three problems are the real difficulties of the "limestone method" of desulfurization, and whether these three problems can be solved is the key to whether the process can achieve its intended goal and whether the device can operate stably.
Fourth, the cycle of bridge theory since it is a natural danger should build a bridge to get over it, after research found that the integration of desulfurization denitrification and dust removal technology has a bridge role. The integration technology of desulfurization, denitrification and dust removal, the environmental protection technology field of flue gas purification technology. It is through the smoke and water mixer using the principle of secondary injection of smoke into the water, the flue gas and water in the uniform dissolver will be fully and uniformly mixed and dissolved, so that the fly ash and particles in the flue gas by water moisture and precipitation, harmful gases dissolved in water, the use of chemical methods to remove SO2, NOX and dust in the flue gas. This method is achieved by the working principle diagram shown in the attached figure. It has 100% dust removal efficiency; >98% desulfurization efficiency; >90% de-selling efficiency. It has a flue gas mixer that is also an induced draft fan. It is suitable for the flue gas purification technology project of coal-fired (steam and oil) boilers and various industrial kilns, etc. The system has simple structure, low cost, high performance to price ratio, energy saving, high temperature resistance and long life.
Technical characteristics of the system Introduction 1) Simple structure and less equipment (as Figure 1) flue gas and water mixer: consists of a water jet pipe and a Rafael jet pipe, forming a secondary injection mechanism. Used to draw the flue gas into the water. Uniform dissolver: is a kind of smoke washing equipment, used to dissolve all the smoke in weak alkali water, dust is wetted by water and become heavy, harmful gases and alkali chemical reaction to generate salt. Water pump: power equipment. Water pool: upper pool, sedimentation pool and lower water bleeding pool. 2) Suitable for a variety of processes (see annex for details) waste discard method: applicable to various sizes of coal-fired (oil, gas) boilers; small sulfur content in coal combustion; the use of desulfurization denitration and dust removal integration process. Lime, limestone as desulfurization agent. Recovered gypsum method: applicable to various specifications of coal-fired (oil, gas) boilers; large sulfur content in coal combustion; integrated process flow of desulfurization, denitrification and dust removal is adopted. Lime is used as desulfurization agent. Recovery fertilizer method: Applicable to various sizes of coal-fired (oil and gas) boilers with large sulfur content in coal combustion; using desulfurization, denitrification and dust removal integrated process. Gas ammonia, ammonia or solid ammonium bicarbonate as absorbent. Dust removal efficiency 100%; desulfurization efficiency > 97%; denitrification efficiency > 90% or more. Suitable for industrial kilns such as steel mills and cement plants. High temperature resistant long life. 3) Anti-corrosion measures Solution configuration: The solution is configured to be alkaline, avoiding the presence of acid in the solution. As shown in Figure 1, dilute alkali solution is continuously and evenly added to the upper pool circulation solution to keep its PH value between 8-9. The alkali in the alkali solution in the uniform dissolver reacts with the acidic oxides such as SO2 in the flue gas to produce salt. The PH value of the solution in the precipitation tank is kept between 7-8. The solution remains weakly alkaline with minimal corrosion. Select acid and alkali resistant materials: stainless steel, ceramics, refractory materials and other wear-resistant acid and alkali resistant materials. The PH value of the solution is monitored and monitored automatically. 4) The waste exclusion system is designed as a round sedimentation tank with a funnel-shaped bottom, and a sediment collector is installed so that the slurry with large concentration is concentrated in the funnel and pumped out with a slurry pump. The waste water in the slurry is clarified and recycled. The discards are used for construction materials, gypsum for industry, and fertilizer for agriculture.
V. Working principle of gypsum method The front stage is used for dry dust collector (such as electric dust collector, etc.) to remove >90% of dust, which is easy to recycle, and the back stage adopts integrated technology of desulfurization, denitrification and dust removal (this program), with 100% dust removal efficiency; desulfurization efficiency >97%, denitrification efficiency >90%, and converts SO2 into gypsum. 1. Process flow diagram of gypsum method
2、The chemical reaction equation is as followsCa(OH)2+SO2=CaSO3+H2O2CaSO3+O2=2CaSO4CaSO3+1/2H2O=CaSO3-1/2H20CaSO4+2H2O=CaSO4-2H2OCaSO3 -1/2H20+O2+2H2O=2CaSO4-2H2ONO+NO2+H2O+O2=2HNO3Ca(OH)2+2HNO3=Ca(NO3)2+H2O
Sixth, the recovery of fertilizer method (ammonia - ammonium sulfite method) applicable to various specifications of coal-fired (oil, gas) boilers; coal-fired with large sulfur content; the use of desulfurization denitrification dust removal integration, dust collector efficiency of 100%; desulfurization efficiency > 98%; 90% of the efficiency of the removal of 90% process flow. Gas ammonia, ammonia or solid ammonium bicarbonate as absorbent.
Process flow diagram 1, solid ammonium bicarbonate as ammonia source process flow diagram as follows.
2、The process flow chart of ammonia as ammonia source is as follows.
3, desulfurization process flow description of the chemical reaction equation is as follows: 2NH4HCO3 + SO2 = (NH4)2SO3 + H2O + 2CO2 (A) (NH4)2SO3 + SO2 + H2O = 2NH4HSO3 (B) absorption process to (B) formula, and 2NH4HSO3 in the generation process is only replenished into the absorption system to make part of the 2NH4HSO3 is regenerated into (NH4)2SO3 to keep the circulating absorption solution alkalinity (SO2/NH3) basically unchanged. If there is oxygen in the flue gas, then (NH4)2SO3+O2/2=(NH4)2SO4. usually there is a small amount of SO3 in the flue gas, then there is: NH4HCO3+SO2+H2O=(NH4)2SO4+ NH4HSO3. NH4HSO3 is acidic. It needs to be neutralized by adding solid ammonium bicarbonate to convert NH4HSO3 to (NH4)2SO4; NH4HSO3+ NH4HCO3= NH4HSO3-H2O+CO2 (C) (C) The formula is a heat absorption reaction and the solution can be reduced to about 0°C without cooling. Since (NH4)2SO3 is more soluble than NH4HSO3 in water, the solution is supersaturated with NH4HSO3-H2O crystals precipitated, and this solution is separated by centrifugation to produce solid ferrous iron.
Seven, the process of denitrification process description 1, what is denitrification? The so-called denitrification refers to the removal of NOX in the flue gas, NOX is mainly composed of NO and NO2, and NO content accounts for more than 90%. To remove NO and NO2 in the flue gas, it is necessary to study the nature of NO and NO2. NO is an inert oxide, which is soluble in water but can not generate nitrogen oxygenated acid. At 0℃, one volume of water can dissolve 0.07 volume of NO. the most special chemical property of NO is addition, which can combine with oxidation in air at room temperature to produce red-brown NO2. NO is unstable, and O2 meet, can make O2 split into oxygen atoms, and combine with one of the oxygen atoms to form NO2. NO2 is red-brown gas with special odor, and polymerize at about -10℃ to form NO2 is a strong oxidizer, it can oxidize SO2 to SO3. NO2 dissolves in water to produce nitric acid and nitrite. NO2 is 5 times more toxic than NO.
How are NO and NO2 produced? Normally N2 and O2 do not undergo a chemical reaction. Nitrogen oxides are generated during the discharge of air or in the process of high temperature combustion, firstly NO is generated, then NO is oxidized to NO2. In the process of high temperature combustion, nitrogen in the air and nitrogen compounds in the fuel and other substances that cannot be burned react chemically with oxygen, firstly NO is formed, then part of it is combined with oxidation in the flue to form NO2, most of the NO is discharged into the atmosphere from the chimney and combined with oxygen in the atmosphere to form NO2. The NO that has not been oxidized to NO2 will coexist with NO2 in the atmosphere. The higher the temperature of the combustion gas during the combustion process, the more excess air, the more NO will be formed. That is, the higher the combustion efficiency, the more easily NO is generated. This combustion method generates more than 90% of NO in NOX and less NO2. According to the common combustion method. The content of NOX in the combustion products of coal is 500-1500ppm.
2、Wet denitrification Denitrification methods are divided into dry and wet methods. Dry denitrification efficiency is about 80%, and the cost is higher. Here the wet denitrification method is used. NO2 dissolved in water to generate nitric acid and NO: 3NO2 + H2O = 2HNO3 + NO when there is enough oxygen: 4NO2 + O2 + 2H2O = 4HNO3NO although dissolved in water, but can not generate nitrogen oxygenated acid. At 0 ℃, one volume of water can dissolve 0.07 volume of NO. NO is difficult to dissolve in water to become a difficult point of denitrification. But in the "integrated technology of desulfurization, denitrification and dust removal" there is enough water to make NO dissolve in water, the relevant research shows that when the content of nitric acid in aqueous solution > 12%, the solubility of NO is 100 times greater than in pure water, that is, a volume of water can dissolve 7 volumes of NO. Let the flue gas start to dissolve in water when the water is pure, first of all, NO2 dissolved in If NO2 is not reduced in water, according to the ratio of flue gas to water in the "integrated technology of desulfurization, denitrification and dust removal", after 2 hours and 44 minutes, the content of nitric acid in water solution will be about 12%. Therefore, it can be said that NO dissolved in water is not a problem.
Since both NO and NO2 have been dissolved in water. The reduction method is used to reduce them to N2 gas. The reducing agent used in the reduction method is (NH4)2SO3 and NH4HSO3, which are the products of the ammonia desulfurization process. The reducing agent is then already in solution and denitrification is already quietly taking place in the homogeneous dissolver. Because the amount of NOX in the flue gas are small, the amount of reducing agents (NH4)2SO3 and NH4HSO3 is sufficient. If the amount of NOX cannot be reduced in its entirety, the remaining part will become NH4NO3 to be left in solution and (NH4)2SO4 to be separated from the solution together as fertilizer. They chemical reaction equation is: 2NO + O2 = 2NO2 + 27 kcal NO + NO2 + H2O = 4HNO2NO2 + 2H2O = HNO2 + HNO34NO2 + O2 + 2H2O = 4HNO3NH3 + HNO3 = NH4NO3NH3 + HNO2 = N2 + 2HONH4OH + HNO3 = NH4NO3 + H2ONH4OH+HNO2=N2+3H2O
NO+NO2+3(NH4)2SO3=N2+3(NH4)2SO4
NO+NO2+3NH4HSO3=N2+3NH4HSO4
4NO2+H2O+3(NH4)2SO3=N2+3(NH4)2SO4+2HNO3
4NO2+H2O+3NH4HSO3=N2+3NH4HSO4+2HNO3
NH4OH+NH4HSO4=(NH4)2SO4-H2O
3、Effect of desulfurization and denitrification and dust removal
1)Desulfurization rate: 98%
2)Denitrification rate: 90%
3)Dust removal efficiency: 100%
Eight, technical process characteristics
(1) The cost and operation cost are very low, and the operation and management workload is very little.
(2) The process is simple, and the whole process can be controlled automatically.
(3) Few measurement and control parameters (PH value, temperature, liquid level), and mature measurement and control technology.
(4) Each process has mature technology to draw on.
(5) Suitable for power stations and industrial boilers of various scales.
(6) Good adaptability to various kinds of sulfur-containing coal (oil).
(7) No adverse impact on the combustion device, production process, raw material sources and product application to the surrounding enterprises without dependence.
(8) conducive to the absorption and utilization of flue gas waste heat.
(9) Does not cause (water, noise, dust, etc.) secondary pollution.
(10) Desulfurization, denitrification and dust removal are completed in the same device. One-time investment, desulfurization rate of 98%, denitrification rate of more than 90%, dust removal rate of 100%, all can be carried out to meet the standard emissions.
(11) Low operating cost. Reduce the operating cost by about 50%-80% than the traditional desulfurization method.
Nine, flue gas desulfurization to reduce costs
The biggest problem with the current flue gas desulfurization technology is the complexity of the technology, high cost and large operating costs. A 300MW (300,000 kW) generating unit flue gas desulfurization, generally using a more mature limestone - gypsum wet flue gas desulfurization, desulfurization efficiency of about 95%, reducing sulfur dioxide emissions of about 10,000 tons per year, each 10,000 tons of sulfur dioxide removal capacity construction investment of about 1 ~ 150 million yuan, power plant flue gas desulfurization facilities operating power consumption is large, a year of desulfurization agent, electricity and labor and other operating The cost is about 16 million yuan, and the cost of desulfurization is about 0.03 yuan per kilowatt-hour, while the subsidy for desulfurization in the feed-in tariff is only 0.015 yuan. At present, most boilers of tens of tons use double alkali method, and in recent years, the sales price of caustic soda (used as flue gas desulfurization agent) has increased exponentially, and the operating cost of desulfurization has increased significantly. Under the double pressure of coal price increase of more than 50% and competitive price on the Internet, coupled with the large gap of desulfurization subsidies, whether the high cost of desulfurization facilities can adhere to normal operation is facing a serious test.
China's desulfurization industry is often faced with high operating costs of desulfurization, the state subsidized desulfurization tariff, can not make the desulfurization device to run at cost, the use of this technology can make the current desulfurization system due to high operating costs and discontinued SO2 purification equipment to run, truly realize the denitrification operating costs "zero" investment, no cost, significantly reduce operating costs It can save a lot of water resources, save power plant traditional desulfurization technology due to wear and tear, serious scaling, complex system, supporting equipment, maintenance workload, and desulfurization system due to (lime milk method) desulfurization clogging, scaling, corrosion, wear and tear, high operating costs, high power consumption to the plant caused by the huge losses, really realize energy saving and emission reduction, improve efficiency, can cancel slurry circulation pump, cancel oxidation fan, cancel slurry system This desulfurization method, compared with the traditional (lime milk) desulfurization method, has a desulfurization efficiency of more than 98%, denitrification efficiency of more than 90%, and can reduce operating costs by 50%-80%, which is an innovation and a major breakthrough in the field of desulfurization, and is the first of its kind at home and abroad. No matter for low sulfur coal, medium sulfur coal, high sulfur coal, can achieve equivalent effect with the traditional (lime milk) method of desulfurization, to achieve zero investment in desulfurization system operating costs, no cost desulfurization, desulfurization tower discharge of the absorption solution, reuse, recycling desulfurization, that is, save a lot of water resources, but also reduce the blockage and scaling of the desulfurization system equipment system pipeline, eliminating the traditional wet desulfurization process in the huge slurry system, eliminating The complete system is greatly simplified and the investment in equipment is greatly reduced.
Ten, flue gas desulfurization technology comparison
Compared with the traditional lime milk desulfurization method of desulfurization, that is, to solve the problem of large water consumption, waste of water resources, the system is easy to scale, clogging, etc., but also to solve the problem of removing SO2 in the flue gas, killing two birds with one stone, desulfurization efficiency of more than 97%, denitrification efficiency of more than 90%, dust removal rate of 100%, no large investment in the construction of denitrification equipment, no cost, significantly reduce operating costs, improve economic efficiency, truly To achieve energy saving and emission reduction, circular economy, turning waste into treasure, to achieve national sustainable development.
Eleven, socio-economic significance
Wet desulfurization technology is the most commercially advantageous desulfurization technology, "integrated technology of desulfurization, denitrification and dust removal" makes it possible to miniaturize and popularize (wet) flue gas desulfurization equipment and devices, and makes it possible to popularize the application of SO2 pollution control in some countries and regions with poor economic conditions. Its economic, high-efficiency, energy-saving, environmental protection, centralized control features and advantages are conducive to the acceptance of many enterprises, making due contribution to the sustainable development of the economy and the progress of environmental science and technology.
Previous:Nothing