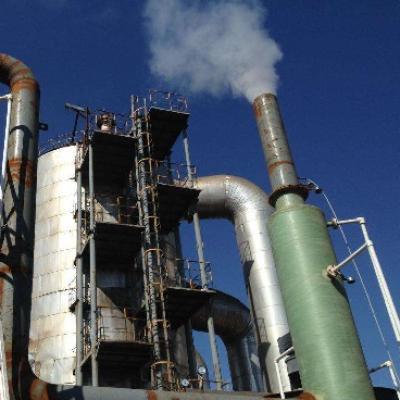
Smart Factory Solution - Digital Twin
Date:2023-01-06 10:33:07 Hits:1181 Belong to:Industrial production
Relying on Shengda cloud platform, Shengda Electric builds a virtual factory, drives the virtual factory with real-time data, and realizes the twin reproduction of the wisdom factory; connects the multi-dimensional data of the information platform, realizes the integrated control of the wisdom factory based on the digital twin, and creates an intelligent, digital and futuristic wisdom factory through the 4 construction stages of the digital twin. Let the production process be known at a glance, let the production data be accurate and credible, and let the control data be within reach.
Sundar Electric has planned the future R&D in accordance with the existing R&D power combined with the existing actual cases of digital twin and the previous R&D direction. The digital twin construction is mainly divided into four stages for the four stages of digital twin: description, diagnosis, prediction and decision.
.png)
1. Accurate mapping, full domain awareness
The first stage of digital twin is mainly to build a virtual space and realize accurate mapping, based on the production logic and process flow of intelligent manufacturing factories, oil fields, military industries, etc. Based on the theory related to the combination of reality and imaginary, the twin in the virtual space is built, including hardware, software and upper system docking interface development, which can correctly and intuitively display the real operation state of the physical world under the drive of data, and realize Accurate virtual-real mapping, comprehensive data perception, and building the base of the digital twin.
2. Dynamic analysis, control the overall situation
The digital twin system puts higher requirements on dynamic data perception technology. In order to establish an all-domain and all-time IOT perception system and realize multi-dimensional and multi-level accurate monitoring of the operation of physical objects, the perception technology not only needs more accurate and reliable physical measurement technology, but also needs to consider the cooperative interaction between perception data, clarify the spatial location and unique identification of objects in the whole domain, and ensure that the devices are credible and controllable. At the same time, dynamic data analysis based on real-time data makes data analysis more timely, makes data more effective, makes guidance more accurate, and achieves more comprehensive control. Real-time dynamic data sensing as well as dynamic data analysis provide an all-round data base for the next stage of construction, laying the foundation for the evolution of the digital twin.
3. Prediction and early warning, integrated decision-making
Prediction means that through data collection, data mining, and data analysis, we can issue forecasts and warnings for risks that already exist, for example, before equipment failures occur, we can alert through early warnings; prediction means that based on the vertical time axis, we can judge certain problems in a relatively long period of time and thus form guidance, for example, for the production process, there may be product accumulation or other production problems at a certain station in a certain period of time For example, for the production process, there may be product accumulation or other production problems at a certain station at a certain time; the first phase and the second phase of data accumulation, data learning, data analysis, combined with the platform algorithm to achieve prediction and early warning, to ensure accurate guidance for decision-making, reduce the downtime of the site, contain the problem before it occurs, and reduce risk.
4. Simulation verification, closed-loop optimization
Simulation in the digital twin system, as a real-time data simulation technology, will contain deterministic laws and complete business process models into a software approach to simulate the physical world. The established validation data and results can be obtained by inputting the corresponding parameters, such as validating the capacity, verifying the balance rate of the production line, reducing the production cycle of new products, and reducing the R&D cost of enterprises.
The iterative relationship between digital twin and simulation technology ensures that the calculation of the simulation is combined with the current state of production, but can also be presented intuitively through the model, allowing the digital twin to truly live and think.
Next:Nothing